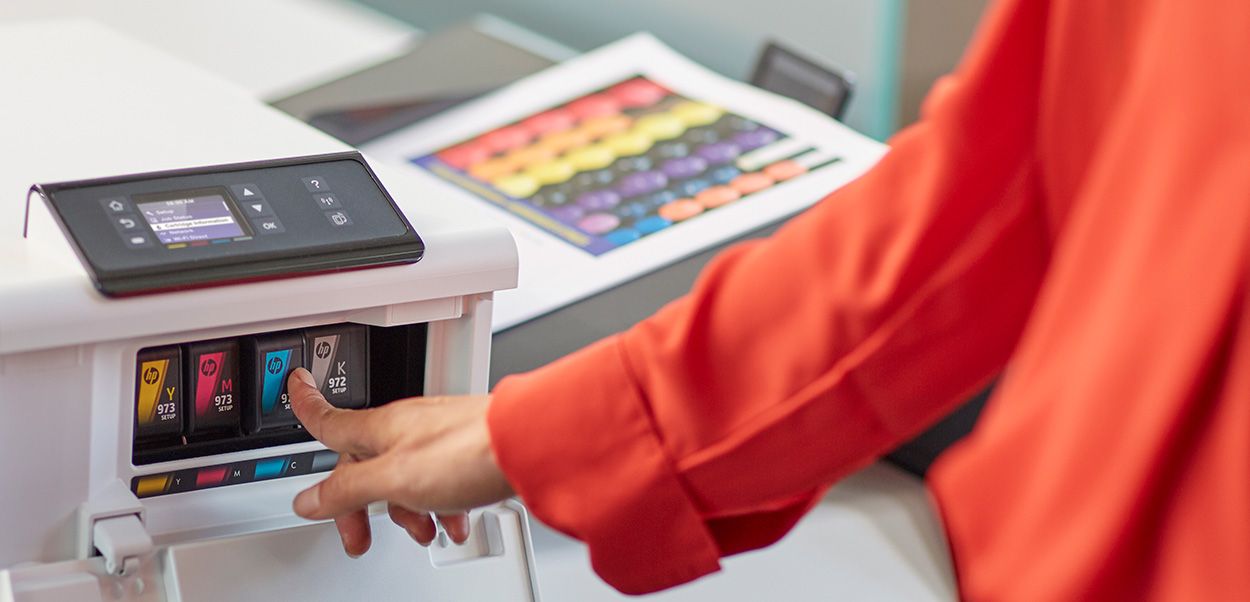
In commercial printing, ink is one of the fundamental consumables that can be managed to diminish costs. All industrial printing managers are searching for ways of controlling this cost. This applies to industrial inkjet printing just as simple printing, as flexo printing or offset printing.
Applying the exact amount of ink necessary to create your necessary printing results is the undeniable way of saving money on this budget detail, yet there are additional advantages that additionally affect and improve on the primary concern for industrial printers.
Cost Benefits of Using Less Ink
There are many additional benefits of reducing ink usage that also improve the bottom line, including some ways to achieve savings that apply to industrial inkjet printing and other commercial printing systems:
1. Shorter Drying Time
Less ink on the substrate leads to shorter drying times. That’s especially important if using an external ink curing system such as LED-light or UV-light. These savings add up to less energy use and increased life of the lighting system. The same is true for heat curing systems.
2. High Production Speed
Production managers should forfeit production speed to guarantee the substrate has been cured completely. With less ink utilized and a more limited drying time, print jobs can be finished quicker. That makes a more prominent printing capacity or diminished work costs.
3. The Environment Benefits of Using Less Ink
As more brands hope to lessen their ecological impact in view of expanding guideline and buyer interest, they are going to their providers to add to maintainability endeavours.
For inkjet printing, less ink consumption reduces the natural resources needed to produce the ink, the number of cartridges used, and the energy needed during printing. All of this contributes to the sustainability of inkjet printing, reducing its environmental impact and increasing cost savings throughout the supply chain.
4. Less Ink Optimises Quality
While it seems counterintuitive, using less ink through optimization can improve printing results. The reality is that too much ink can negatively impact quality as much as too little ink.
Dot Gain
The preparation of image files must account for the type of substrate being used and ink to compensate for dot gain, which is more pronounced on porous substrates. Dot gain, or tone value increase (TVI) is the spread of the ink in the halftone dots as the ink is absorbed. Colour profiles for different substrates account for the expected dot gain. Too much ink will make the printed image look darker than intended because the light is not reflected from the “white space” between the dots.
Bleed Through
Beside the negative effect of dot gain on image quality, too much ink on the substrate can result in bleed-through. In the case of thin, porous substrates, printing with too much ink can impact the reverse side of the printing material when the ink is absorbed.
How to Optimize Ink Usage For Savings
Added together, the combination of actions can lead to 20-30% reduction in ink consumption.
1. Choose The Right Printing Resolution
Although it's enticing to use the highest resolution the printer can deliver. Just because a printhead can lay down ink at 600 dpi it doesn’t mean it is necessary. In the case of barcodes and matrix codes, high resolution may be necessary to avoid scanning errors, but other jobs may only require a significantly lower resolution. That’s where dot gain can work to your advantage. Only use the resolution necessary to achieve the quality needed by the customer. Digital inkjet printing offers the distinct advantage of testing samples to determine the best results because there are no costly prepress expenses of plates.
2. Choose Grey Component Replacement
Black ink is your friend. When printing four-colour (CMYK) projects, ink consumption can be drastically reduced. Rather than creating grey tones with trichromatic colours layers of cyan, magenta, and yellow inks, the black ink in CMYK can often achieve the same result.
An added benefit is greater edge definition. Unless it is absolutely necessary to have the richest black tonal range, GCR can deliver significant savings.
3. Use Eco-fonts For Typography
Consult with the designer to identify fonts that can reduce ink consumption. A client may require specific typefaces to maintain brand identity, but there may be opportunities to reduce ink consumption with an “eco-font” for some print jobs where those branded typefaces may not be necessary.
Light-face fonts and sans-serif fonts can deliver incremental ink savings, especially on larger jobs such as transactional documents. When evaluating the impact of choosing a different typeface, be sure to consider the readability of the text.
4. Other Steps of Conserving Ink:
Taking Care of Printheads
Industrial printing inks with a short decay can result in wasted ink. When the ink dries in the print head, purging and cleaning wastes ink. This is especially problematic for TIJ printing with solvent ink, which has notoriously suffered from short decay times. Kao Collins has solved that problem with the revolutionary SIGMA solvent ink. It's 12-hour decap time far exceeds any other solvent inkjet ink.
Use Original Print Cartridges
All the initial savings of using non-original cartridges can be lost when these cartridges fail, and you’re left with ink inside that can’t be used. That’s one reason Kao Collins packages inks for HP and Funai industrial printing systems in original, factory-new cartridges.
Install Bulk Ink Systems
Small amounts of ink remaining in single cartridges add up during the production cycle. Bulk supply systems reduce unused ink. Bulk systems also increase efficiency.
Data Drives Decisions
Carefully tracking the yield of cartridges or bulk ink delivery helps you analyse the steps you’re taking to reduce ink consumption and overall production. Choosing the right ink for the substrate is equally important for achieving optimum quality and production efficiency.